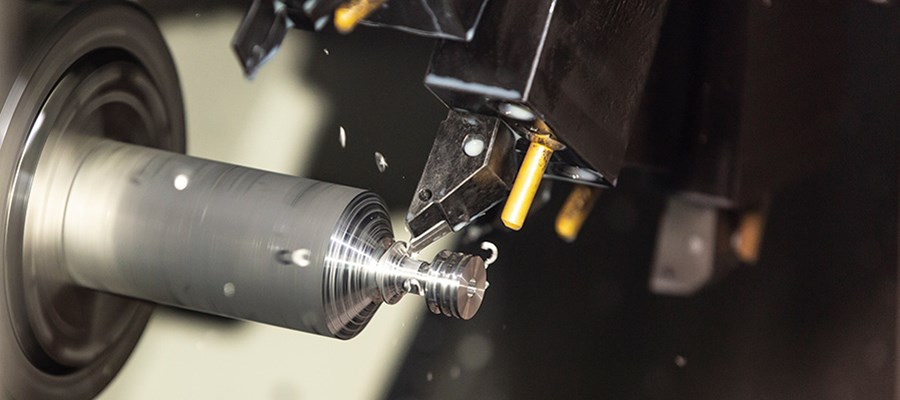
Ensimmäinen asia, josta puhutaan, on titaaniseoksen käsittelyn fyysinen ilmiö.Vaikka titaaniseoksen leikkausvoima on vain hieman suurempi kuin saman kovuuden omaavan teräksen leikkausvoima, titaaniseoksen prosessoinnin fysikaalinen ilmiö on paljon monimutkaisempi kuin teräksen käsittelyssä, mikä vaikeuttaa titaaniseoksen käsittelyä.
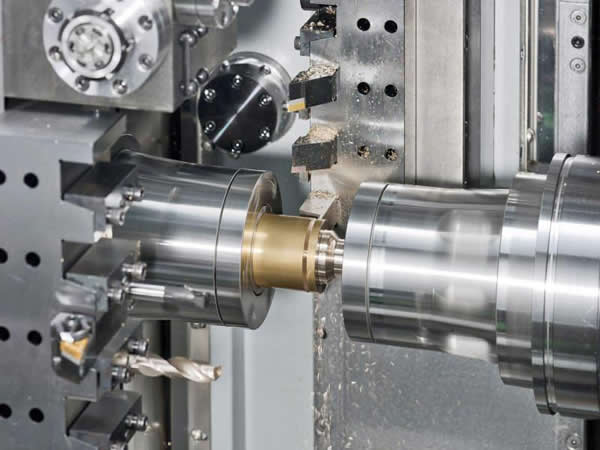
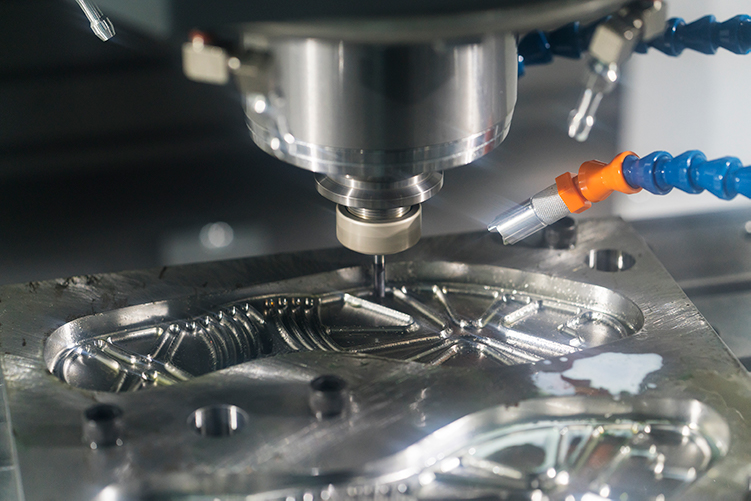
Useimpien titaaniseosten lämmönjohtavuus on erittäin alhainen, vain 1/7 teräksestä ja 1/16 alumiinista.Siksi titaaniseosten leikkaamisessa syntyvä lämpö ei siirry nopeasti työkappaleeseen tai ota pois lastut, vaan se kerääntyy leikkausalueelle ja syntyvä lämpötila voi olla jopa 1 000 °C tai enemmän. , mikä aiheuttaa työkalun leikkuureunan nopean kulumisen, halkeilun ja halkeilun.Kerääntyneen reunan muodostuminen, kuluneen reunan nopea ilmaantuminen puolestaan tuottaa enemmän lämpöä leikkausalueelle, mikä lyhentää entisestään työkalun käyttöikää.
Leikkausprosessin aikana syntyvä korkea lämpötila tuhoaa myös titaaniseososien pinnan eheyden, mikä johtaa osien geometrisen tarkkuuden heikkenemiseen ja työkarkaisuilmiöön, joka heikentää merkittävästi niiden väsymislujuutta.
Titaaniseosten elastisuus voi olla hyödyllistä osien suorituskyvylle, mutta leikkausprosessin aikana työkappaleen elastinen muodonmuutos on tärkeä tärinän aiheuttaja.Leikkauspaine saa "elastisen" työkappaleen siirtymään pois työkalusta ja pomppimaan siten, että työkalun ja työkappaleen välinen kitka on suurempi kuin leikkaustoiminto.Kitkaprosessi tuottaa myös lämpöä, mikä pahentaa titaaniseosten huonon lämmönjohtavuuden ongelmaa.
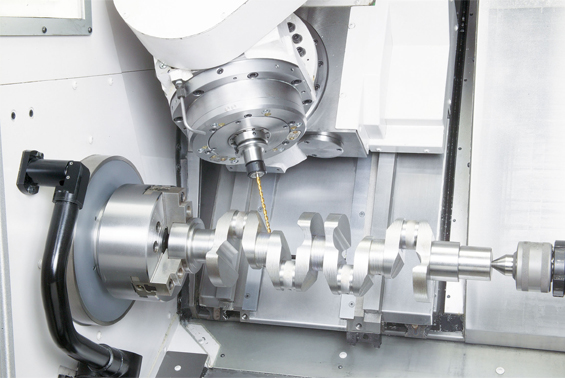
Tämä ongelma on vielä vakavampi, kun käsitellään ohutseinäisiä tai renkaan muotoisia osia, jotka ovat helposti muotoaan.Titaaniseoksen ohutseinäisten osien käsittely odotettuun mittatarkkuuteen ei ole helppoa.Koska kun työkalu työntää työkappaleen materiaalia pois, ohuen seinän paikallinen muodonmuutos on ylittänyt elastisen alueen ja tapahtuu plastista muodonmuutosta, ja materiaalin lujuus ja leikkauspisteen kovuus kasvavat merkittävästi.Tässä vaiheessa koneistus aiemmin määritetyllä lastuamisnopeudella tulee liian suureksi, mikä edelleen johtaa terävään työkalun kulumiseen.Voidaan sanoa, että "lämpö" on "perussyy", joka vaikeuttaa titaaniseosten käsittelyä.
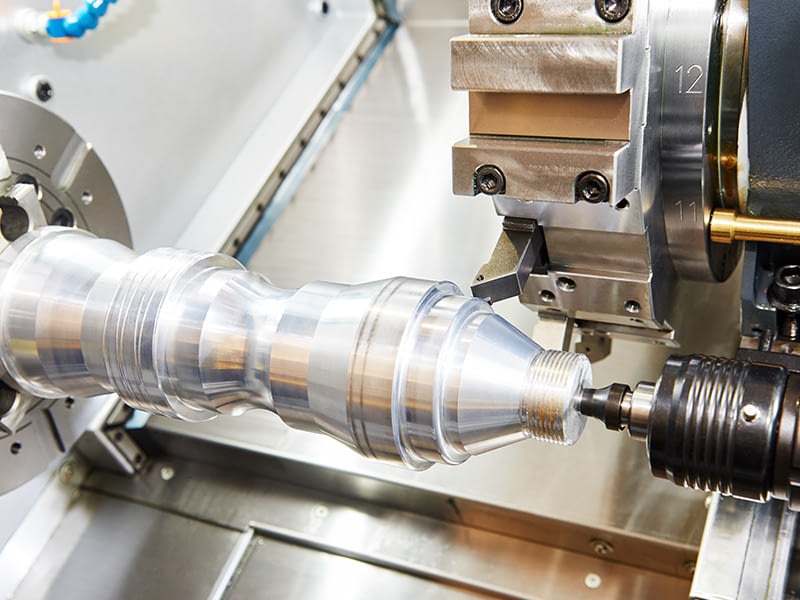
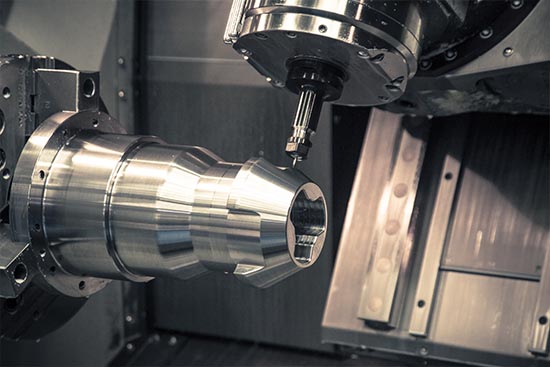
Leikkaustyökaluteollisuuden johtavana yrityksenä Sandvik Coromant on huolellisesti koonnut prosessiosaamisen titaaniseosten käsittelyyn ja jakanut sen koko teollisuuden kanssa.Sandvik Coromant sanoi, että titaaniseosten käsittelymekanismin ymmärtämisen ja aiemman kokemuksen lisäämisen perusteella titaaniseosten prosessointiprosessin pääasiallinen osaaminen on seuraava:
(1) Positiivisen geometrian omaavia teriä käytetään vähentämään leikkausvoimaa, leikkauslämpöä ja työkappaleen muodonmuutoksia.
(2) Pidä jatkuvaa syöttöä työkappaleen kovettumisen välttämiseksi, työkalun tulee aina olla syöttötilassa leikkausprosessin aikana ja radiaalisen leikkausmäärän ae tulee olla 30 % säteestä jyrsinnän aikana.
(3) Korkeapaineista ja suuren virtauksen leikkausnestettä käytetään varmistamaan koneistusprosessin lämpöstabiilisuus ja estämään työkappaleen pinnan rappeutuminen ja työkaluvauriot liiallisesta lämpötilasta.
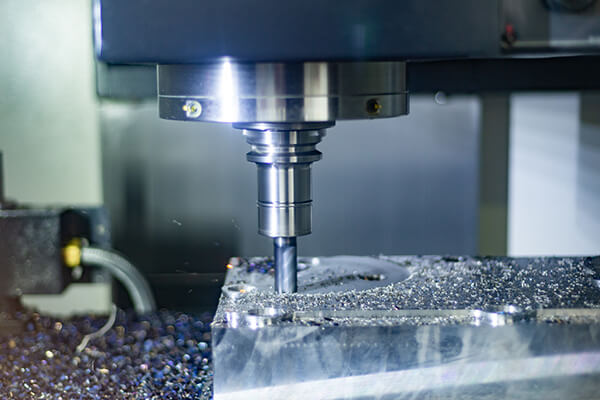
(4) Pidä terän reuna terävänä, tylsät työkalut aiheuttavat lämmön kertymistä ja kulumista, mikä voi helposti johtaa työkalun rikkoutumiseen.
(5) Työstö titaaniseoksen pehmeimmässä tilassa mahdollisimman paljon, koska materiaalista tulee vaikeampi työstää kovettumisen jälkeen ja lämpökäsittely lisää materiaalin lujuutta ja lisää sisäkkeen kulumista.
(6) Käytä suurta kärjen sädettä tai viistettä leikkaamiseen ja laita mahdollisimman monta leikkuureunaa leikkaukseen.Tämä vähentää leikkausvoimaa ja lämpöä joka pisteessä ja estää paikallisen rikkoutumisen.Kun jyrsitään titaaniseoksia, lastuamisparametreista leikkausnopeus vaikuttaa eniten työkalun käyttöikään vc, jota seuraa säteittäinen lastuamismäärä (jyrsintäsyvyys) ae.
Postitusaika: 06.04.2022